Pipeline Welding 101
Pipeline welding joins sections of pipes to ensure the continuous transport of key resources like water and oil. It’s vital in construction, oil, natural gas utilities, and gas, and more. This article covers the techniques, skills, and career insights for pipeline welding.
Key Takeaways
Pipeline welding is critical for infrastructure construction, impacting economic sustainability and essential resources like water and oil, especially in oil refineries.
Key welding methods include Shielded Metal Arc, Flux-Cored Arc, and Submerged Arc welding, each with distinct advantages and challenges.
Aspiring pipeline welders should focus on hands-on training, equipment maintenance, and understanding safety regulations to excel in their careers.
Understanding Pipeline Welding
Pipeline welding, also known as girth welding, is the process of joining pipes to create a continuous and extensive network. It plays a crucial role in maintaining essential resources such as water and oil, significantly contributing to infrastructure development. Beyond its structural importance, pipeline welding also impacts economic sustainability by influencing profitability for future generations.
Pipeline welding is utilized across various industries, from construction and oil and gas fields to water industries, fabrication shops, and nuclear power. It is also a specialized skill in sectors like aerospace, nuclear, and auto manufacturing. The primary purpose is to join two pipes together, ensuring uniformity and durability in the pipeline network. Gas tungsten arc welding is known for its high-quality welds and suitability for critical jobs.
Excelling in pipeline welding requires proficiency in multiple welding positions, thorough knowledge of pipeline construction and maintenance, and strict adherence to safety regulations. These skills are fundamental to ensuring the integrity and longevity of the welded pipes, which are often subjected to harsh industrial environments.
Definition and Overview of Pipeline Welding
Pipeline welding is a specialized process used to assemble and maintain pipelines that transport various substances such as oil, natural gas, and water. This intricate task involves joining pipes using a variety of welding techniques, including shielded metal arc welding (SMAW), flux-cored arc welding (FCAW), gas metal arc welding (GMAW), and submerged arc welding (SAW). Each method has its unique advantages and is chosen based on the specific requirements of the job.
Pipeline welding demands highly skilled welders who can adapt to challenging environments and conditions. These professionals often work in remote locations and face extreme weather, making resilience and adaptability crucial traits. The ability to perform precise and durable welds under such conditions is what sets pipeline welders apart in the field.
Importance of Pipeline Welding
Pipeline welding is indispensable for the transportation of essential resources like oil and natural gas to industries and households. The integrity of these pipelines is paramount to ensure the safe and efficient delivery of these resources. Skilled pipeline welders play a vital role in maintaining this integrity, preventing leaks and ensuring the longevity of the pipeline infrastructure.
Beyond transportation, pipeline welding is crucial in the construction and maintenance of infrastructure such as refineries and power plants. The demand for skilled pipeline welders is high, reflecting the significant impact their work has on the economy and the environment. Their expertise ensures that pipelines operate safely and efficiently, contributing to the overall stability and growth of various sectors.
Key Pipeline Welding Methods
Pipeline welding employs various arc welding techniques, each with its own advantages and applications. The most common methods include Shielded Metal Arc Welding (SMAW), Flux-Cored Arc Welding (FCAW), and Submerged Arc Welding (SAW). Each method has unique characteristics that make it suitable for different welding conditions and requirements. Stovepipe welding is another name for Shielded Metal Arc Welding (SMAW).
Aspiring pipeline welders must understand these methods to be effective in their roles.
Shielded Metal Arc Welding (SMAW)
Shielded Metal Arc Welding (SMAW), also known as stick welding, is a manual process that uses an electric arc to melt electrodes and join metals. Unlike other welding methods, SMAW does not require shielding gas, making it highly portable and flexible. This portability allows welders to work in diverse environments without the need for additional equipment.
However, SMAW has its limitations. Its slow travel speed makes it less productive compared to other techniques. Despite this, its simplicity and versatility make it a popular choice for many pipeline welders, especially in field conditions where other methods might not be feasible.
Flux-Cored Arc Welding (FCAW)
Flux-Cored Arc Welding (FCAW) is particularly suitable for outdoor conditions and windy environments. It utilizes semi-automatic machines, which can enhance productivity and consistency in welding. FCAW is advantageous in situations where shielding gas might be disrupted by wind, as it uses a flux-cored electrode that provides its own shielding.
However, FCAW also has its challenges. Wind can disturb the shielding gas in gas-shielded FCAW, leading to porosity defects in the welds. Despite these challenges, FCAW remains a versatile and effective method for various pipeline welding applications.
Submerged Arc Welding (SAW)
Submerged Arc Welding (SAW) is a semi-automatic process. It involves forming an electric arc between the workpiece and a continuously fed electrode. This method is known for producing flawless surfaces in welds, making it a preferred choice for applications requiring high-quality finishes. The submerged arc ensures that the weld area is protected from contamination, resulting in strong and durable joints.
One of the challenges of SAW is that tracing the joint can be difficult since the arc is not visible during the process. Despite this, SAW is widely used in pipeline construction due to its high deposition rates and efficiency.
Gas Metal Arc Welding (GMAW) Applications
Gas metal arc welding (GMAW) is a widely utilized process in pipeline welding, known for its efficiency and versatility. This method is particularly effective for welding thin-gauge materials like pipes and tubes, making it ideal for high-speed welding applications. GMAW is also favored for welding aluminum and stainless steel pipes, which are commonly used in pipeline construction.
One of the key advantages of GMAW is its high deposition rates, which enhance productivity. Additionally, it generates low fumes, creating a safer work environment for pipeline welders. The ease of use and adaptability of GMAW make it a popular choice in the industry, allowing welders to achieve high-quality welds with consistency.
Essential Skills for Pipeline Welders
Pipeline welders require a diverse set of skills to perform their job effectively. These include:
Physical Strength and Endurance: The ability to work in challenging environments, including extreme temperatures and remote locations, is essential.
Hand-Eye Coordination and Dexterity: Precision in manipulating welding equipment is crucial for creating strong and durable welds.
Ability to Work at Heights and in Confined Spaces: Many pipeline welding tasks require working in difficult positions, necessitating comfort with heights and tight spaces.
Knowledge of Welding Techniques: Proficiency in SMAW, FCAW, GMAW, and SAW is fundamental to performing various welding tasks.
Understanding of Pipeline Construction and Maintenance: Familiarity with the procedures and standards in pipeline construction ensures the integrity of the work.
Safety Regulations and Standards: Adherence to safety protocols is vital to prevent accidents and ensure a safe working environment.
Teamwork and Independence: The ability to work both independently and as part of a team is important for the collaborative nature of pipeline projects.
Physical and Mental Demands
Pipeline welding is a physically demanding profession that requires welders to operate in challenging environments. This includes working in extreme temperatures, remote locations, and confined spaces. Welders must be capable of lifting and carrying heavy equipment, working at heights, and performing repetitive tasks for extended periods.
Mentally, pipeline welders need to maintain focus and concentration for long durations, often under pressure. Quick decision-making in emergency situations is crucial, as is the ability to manage stress and fatigue. The physical and mental resilience required for this job underscores the demanding nature of pipeline welding, highlighting the dedication and skill of those in the profession.
Steps to Start Pipeline Welding
Beginning a career in pipeline welding requires several key steps. Initially, gather essential welding tools like flame torches, shielded metal arc, and tungsten arcs, including gas tungsten arc welding. Once equipped, pursue formal training and certification. Completing a welding program and gaining practical experience through entry-level jobs and apprenticeships are vital for skill development.
Real-world experience is indispensable. Working in remote locations and unpredictable weather conditions builds resilience and adaptability, crucial for managing the complexities of pipeline welding and preparing welders for field challenges.
Gathering Equipment
The essential welding equipment for pipe welding includes flame torches, shielded metal arc, and tungsten arcs, such as gas tungsten arc welding. SMAW is particularly advantageous due to its portability and flexibility, allowing welders to operate in a wide range of conditions without the need for shielding gas.
Maintaining welding tools and field service equipment is a key responsibility. Proper upkeep ensures optimal condition, reducing malfunctions and ensuring weld quality. Regular inspections, repairs, and replacements of worn components are essential.
Training and Certification
Hands-on training is crucial for developing the skills necessary for pipeline welding. Strong mechanical skills and the ability to work in various weather conditions are essential traits for pipeline welders. Accreditation from recognized bodies can indicate the quality of welding schools and their programs. Industry relationships also reflect the credibility and effectiveness of a trade school’s training program.
Education and hands-on training are essential for developing pipeline welding skills. Choosing accredited schools with comprehensive programs that blend theoretical knowledge with practical experience is beneficial.
Pipeline Welder's Job Description
Pipeline welders and pipe welder are responsible for joining, maintaining, and repairing piping systems and components, including those in oil refineries. This includes tasks such as cutting, dismantling, and reshaping pipe sections to ensure they fit perfectly. Precision is vital; minor defects can result in serious failures and expensive repairs.
Pipeline welders must read and interpret blueprints and welding symbols to ensure correct and efficient pipe assembly. Physical strength and problem-solving skills are also important for managing the job’s demands and troubleshooting issues.
Welded pipes offer superior corrosion resistance and high structural integrity, making them ideal for harsh industrial environments and high-pressure applications. Pipeline welders may also conduct ‘hot-tapping,’ which involves welding on live pipelines, adding another layer of complexity to their role. Due to the quicker installation processes, welded pipes can help lower overall labor costs on projects.
Challenges in Pipeline Welding
Pipeline welding presents several challenges, including working in diverse environments, from urban settings to remote areas, often exposed to extreme weather conditions. Health and safety hazards are significant, with welders being exposed to fumes, dust, airborne particles, extreme heat, and harmful light.
Common technical challenges include lack of fusion, slag entrapments, and hydrogen inclusion. Welders must navigate various positions, from 1G to 6G, each with unique challenges in maintaining angle and consistency. Proper preparation, training, and equipment can mitigate these issues. Additionally, stovepipe welding, known for its slower travel speed, can affect productivity.
Benefits of Pipeline Welding
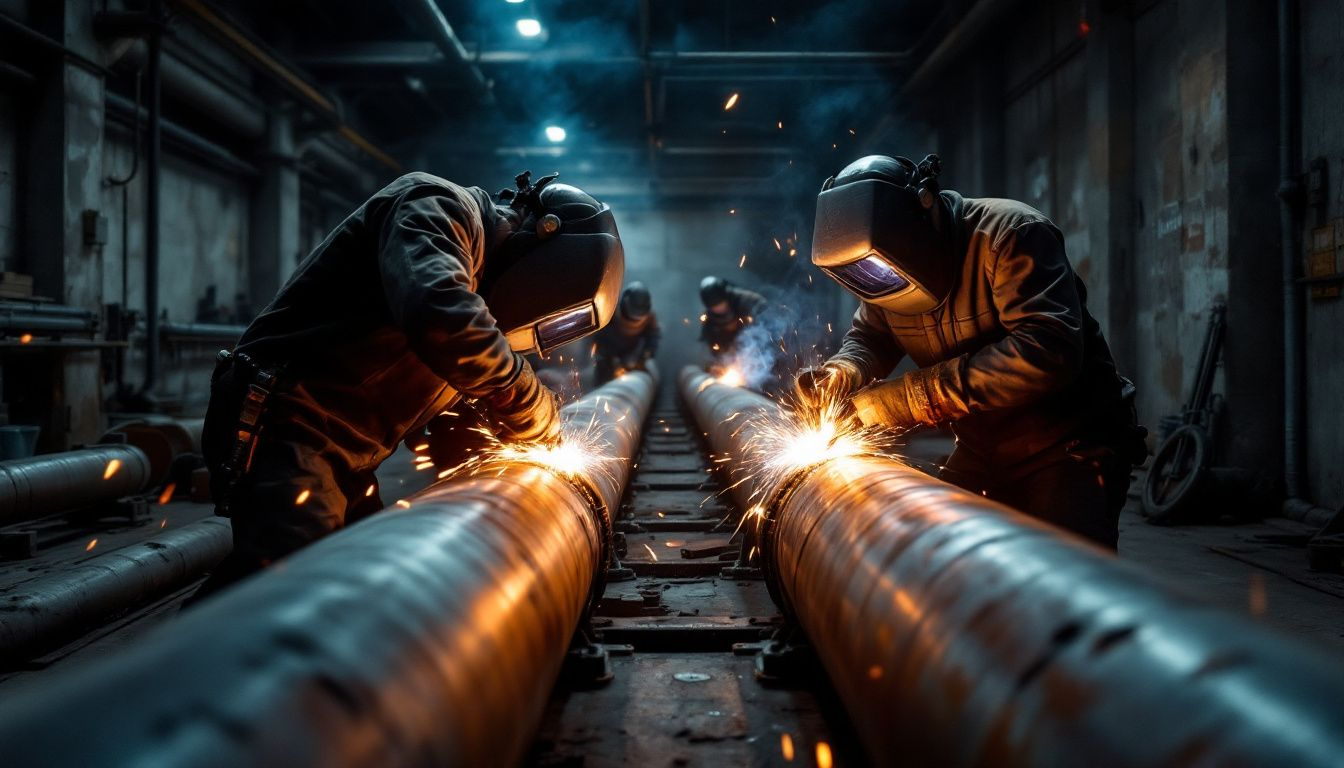
Pipeline welding offers benefits like efficiency and durability. Submerged Arc Welding (SAW) provides the highest deposition rates, enhancing efficiency. Gas Metal Arc Welding (GMAW) increases productivity and generates low fumes, improving the work environment.
Welding pipes are less prone to leaks compared to screwed systems, improving durability and reducing maintenance costs. Welding eliminates the need for pipe fittings, which can weaken connections, thereby enhancing the overall strength and integrity of the welding pipes.
The smooth surfaces created by welded joints improve fluid flow and reduce wear over time, contributing to the long-term efficiency of the pipeline. Natural gas utilities play a significant role in the growing demand for skilled welders, as they are essential for maintaining resources like water and oil.
Career Path and Opportunities
Researching the qualifications needed for pipeline welding roles is essential for aspiring welders. Pipeline welders are highly skilled and sought after due to the complexity of their work. Entry-level positions can earn around $52,000 annually, with the national median salary at approximately $69,000. Highly skilled welders can earn over $100,000, reflecting high demand for their expertise. There is also a growing demand for skilled welders in natural gas utilities, which underscores the importance of this sector.
Pipeline welders often travel extensively for job opportunities, as projects can take place in diverse locations. This travel can be an exciting aspect of the job, offering a pipeline welder the chance to work in various environments and gain a broad range of experience.
Summary
Pipeline welding is a crucial trade that ensures the integrity and efficiency of our essential infrastructure. From understanding the various welding methods to the steps needed to start a career, this blog post has covered the essential aspects of pipeline welding. The responsibilities, challenges, and benefits of being a pipeline welder highlight the importance and complexity of this profession.
For those considering a career in pipeline welding, the opportunities are vast and rewarding. With the right training, equipment, and dedication, you can become a skilled pipeline welder, contributing to vital infrastructure projects and enjoying a lucrative and fulfilling career.
Frequently Asked Questions
What is the welding pipeline?
The welding pipeline, or girth welding, is a fabrication process used to assemble pipes into a network, employing techniques such as flame torches and arc welding by pipeline welders. This process is crucial for creating strong and durable connections in pipeline construction.
Is pipe welding a good career?
Pipe welding is a promising career choice due to high demand, competitive salaries, and numerous opportunities for advancement. This field offers job security and the potential for diverse experiences and travel.
What is the highest salary for a pipeline welder?
The highest salary for a pipeline welder can reach up to $135,000 annually, making them among the top earners in the welding trade. This figure reflects the competitive nature of the profession and the demand for skilled welders.
What is pipeline welding?
Pipeline welding, or girth welding, involves joining pipes to form a seamless network crucial for transporting resources like water and oil. This process plays a vital role in ensuring the integrity and efficiency of infrastructure systems.
What are the key methods used in pipeline welding?
The key methods used in pipeline welding are Shielded Metal Arc Welding (SMAW), Flux-Cored Arc Welding (FCAW), and Submerged Arc Welding (SAW), each tailored for specific conditions and requirements in the welding process.
Lincoln Vantage 500 - Top Choic
The Lincoln Vantage 500 is a top-tier diesel welder/generator favored by professionals for its power and advanced features. In this article, we delve into its technological innovations, performance capabilities, and why it stands out in the field of welding equipment.
Key Takeaways
The Lincoln Vantage 500 is powered by a Perkins diesel engine providing 37.2 horsepower and exceptional fuel efficiency, making it a cost-effective choice for professionals.
With a maximum welding output of 500 amps and multiple process capabilities, including stick or wire welding, the Vantage 500 is versatile enough for various applications including stick, TIG, MIG, and arc gouging.
Its innovative design features, such as easy service access and advanced Chopper Technology, enhance durability, reliability, and overall performance in demanding environments.
Lincoln Vantage® 500 Overview
The Lincoln Vantage 500 is a robust and reliable welding machine powered by a Perkins® diesel engine that delivers an impressive 37.2 horsepower while meeting EPA Tier 4i emissions standards. This powerhouse is designed to deliver optimal fuel efficiency, significantly lowering operating costs and enhancing overall performance, making it a smart investment for any professional welder, especially when compared to other engine driven welders.
What truly sets the Vantage 500 apart is its innovative patented Chopper Technology®. This technology enhances the quality of welds with reduced spatter, resulting in cleaner, more precise welds every time. Whether you’re working on construction sites or in industrial settings, the Lincoln Vantage 500 ensures that your welds are of the highest quality.
In essence, the Lincoln Vantage 500 isn’t just a welder; it’s a comprehensive solution for professionals who demand reliability, efficiency, and top-notch performance. It’s designed to handle the toughest jobs while maintaining superior fuel efficiency and environmental standards.
Superior Welding Output
When it comes to welding output, the Lincoln Vantage 500 is unmatched. This engine-driven welder can deliver a maximum welding output of 500 amps, making it powerful enough for large-scale welding operations. It’s specifically designed to meet the needs of pipe rig owners and construction teams, providing the versatility and power required for diverse welding tasks.
The Vantage 500 offers five basic welding modes: CC-Stick, Downhill Pipe, DC Touch Start TIG, CV-Wire, and Arc Gouging. These modes maximize output and ensure that you can tackle numerous welding applications with ease. Whether you’re engaged in stick or wire welding, the welder generator delivers consistent, high-quality results. The machine’s ability to maintain a maximum open circuit voltage of 60 volts provides the flexibility needed for various welding processes.
Additionally, the DC welding control system utilizes patented Chopper Technology® to enhance welding performance, ensuring smooth material removal and minimizing spatter. This makes the Lincoln Vantage 500 ideal for pipe rig owners who need a reliable and efficient tool that performs exceptionally well in demanding environments.
Compact and Efficient Design
Despite its powerful capabilities, the Lincoln Vantage 500 boasts a compact design that enhances its portability and ease of use on job sites. Weighing approximately 1290 lbs (586 kg), it strikes a perfect balance between being manageable for transport and maintaining a rugged build. This makes it ideal for professionals who need to move their equipment between different job sites regularly.
The compact dimensions and versatile configurations, with up to 525 amps output, make the Vantage 500 effective for a range of welding processes even in confined spaces. Whether you need to perform stick, TIG, MIG, or flux-cored welding, this machine runs smooth and quiet, ensuring that your job site remains productive and efficient.
Enhanced Durability and Reliability
Durability and reliability are at the core of the Lincoln Vantage 500’s design. It features a robust stainless steel enclosure that enhances its ability to endure harsh working conditions. This welder is built to withstand the toughest environments, ensuring reliable operations even under extreme conditions.
One of the standout features of the Vantage 500 is its front battery drawer and lockable sliding access door, which allow for quick and easy access to the battery and internal components. This innovative service access enhances maintenance efficiency and reduces downtime. Additionally, the patented Chopper Technology minimizes spatter and enhances gouging performance, preventing engine stalling and ensuring smooth and reliable operations.
The machine is powered by a durable Perkins diesel engine, specifically engineered to provide reliable operation while minimizing noise. This makes the Lincoln Vantage 500 not only a powerful and reliable welding tool but also one that contributes to a more pleasant working environment.
Fuel Efficiency and Environmental Impact
Fuel efficiency is a critical factor for professionals who rely on their equipment for extended periods. The Lincoln Vantage 500 excels in this area, offering exceptional fuel efficiency that significantly reduces operational costs. This not only makes it a cost-effective choice but also helps in maintaining longer, uninterrupted work sessions without frequent refueling.
Moreover, the Vantage 500’s efficient fuel consumption helps reduce its overall environmental footprint. Minimizing fuel consumption supports sustainable practices, making it a responsible choice for environmentally-conscious professionals and rental fleet managers alike.
Versatile Applications and Multi-Process Capabilities
The Lincoln Vantage 500 is a versatile machine that supports multiple welding process modes, including CC-Stick, Downhill Pipe, DC Touch Start TIG®, CV-Wire, and Arc Gouging. This flexibility makes it suitable for a wide range of applications, from industrial settings to construction and repair tasks.
Its multi-process welding capabilities allow it to handle diverse projects with ease. Whether you are engaged in stick or wire welding, TIG, MIG, or flux-cored welding, the Vantage 500 provides reliable operations and high-quality results in dc multi process welding.
The machine’s ability to generate continuous three-phase auxiliary power up to 14.5 kW further enhances its versatility, enabling it to operate a variety of power industrial equipment tools effectively and in a mode which maximizes output.
With the Lincoln Vantage 500, professionals can confidently tackle numerous welding tasks, knowing they have a reliable and powerful tool at their disposal.
Innovative Service Access and Maintenance
Maintaining the Lincoln Vantage 500 is a breeze, thanks to its innovative service access features. The removable sliding access door allows for easier access to the engine and internal components during maintenance tasks. This user-friendly design element not only simplifies routine checks but also enhances the overall longevity of the equipment.
Moreover, the robust and reliable Perkins industrial diesel engine operates quietly, contributing to a positive user experience. These maintenance-friendly features ensure that the Vantage 500 remains in top working condition, even in challenging job site environments.
Advanced Arc Gouging and Auxiliary Power
One of the standout features of the Lincoln Vantage 500 is its advanced arc gouging mode which maximizes output, enabling efficient removal of materials using carbon rods up to 3/8 inch in diameter. Whether you’re engaged in heavy-duty carbon arc gouging applications or other demanding applications, the Vantage 500 delivers enhanced gouging performance and allows you to experience premium arc performance with consistent results.
In addition to its welding capabilities, the Vantage 500 offers a generator output of up to 14.5 kW, making it capable of powering industrial tools and other equipment on the job site. With its patented Chopper Technology, the Vantage 500 minimizes engine stalling, providing consistent performance during gouging operations and ensuring reliable ac generator power.
This combination of advanced arc gouging and auxiliary power capabilities makes the Lincoln Vantage 500 an indispensable tool for professionals who need to run industrial tools and tackle numerous welding tasks efficiently.
Why Professionals Choose Lincoln Vantage
Professionals choose the Lincoln Vantage 500 for its outstanding arc stability, which is crucial for achieving consistent weld quality. This machine is designed to meet the rigorous demands of professional welders, providing reliable operations and high-quality results in a variety of applications.
With its robust build, advanced technology, and versatile capabilities, the Vantage 500 stands out as the top choice for professionals who need a reliable, efficient, and powerful welding solution.
Summary
In summary, the Lincoln Vantage 500 is a top-tier diesel engine driven welder/generator that delivers exceptional performance, fuel efficiency, and durability. Its powerful output, versatile applications, and user-friendly design make it an ideal choice for professionals across various industries.
If you’re looking for a reliable and efficient welding solution that can handle the toughest jobs, the Lincoln Vantage 500 is the perfect tool for you. Invest in this powerhouse and experience the difference it can make on your job site.
Frequently Asked Questions
Does Lincoln make good welders?
Yes, Lincoln welders are highly regarded for their robust performance and strong DC capabilities, ensuring smooth and consistent welding across various materials.
What kind of engine powers the Lincoln Vantage 500?
The Lincoln Vantage 500 is powered by a Perkins® diesel engine, providing 37.2 horsepower and compliant with EPA Tier 4i emissions standards.
What is the maximum welding output of the Lincoln Vantage 500?
The Lincoln Vantage 500 provides a maximum welding output of 500 amps. This capability makes it suitable for a variety of tough welding applications.
How does the Lincoln Vantage 500 enhance welding performance?
The Lincoln Vantage 500 enhances welding performance through its patented Chopper Technology®, which improves weld quality and minimizes spatter. This results in cleaner and more efficient welding outcomes.
What are the maintenance features of the Lincoln Vantage 500?
The Lincoln Vantage 500 is designed with a removable sliding access door and a front battery drawer, facilitating easier maintenance access. These features ensure that you can service the unit efficiently and effectively.
A Wire Feeder has a wire feed mechanism that pulls wire from the spool and pushes it through the electrode cable liner and out the transfer tube. For GMAW, a solenoid—an electrically operated valve—opens and releases shielding gas from the regulator and flowmeter.FAQ's Welder Generators
What is a welder generator welding machine?
What safety precautions should be taken when using a welder generator?
What are the different types of welder generators?
What are the advantages of using a welder generator?
Featured Products
Top Tips for Choosing the Best Welder Generator for Your Needs
Need a generator welder and not sure which one to pick? Lincoln welder generators provide both welding power and auxiliary power for remote job sites. This guide will help you choose the right engine driven welder for your needs, especially for tasks like pipeline welding, which require reliable and consistent power. Pipeline welding involves joining and repairing pipes that transport liquids and gases, and it demands precision and durability. Choosing the right welder generator ensures that you have the necessary capabilities to handle the complexities of reshaping pipe sections, hot tapping, and maintaining pipeline
Key Takeaways
Welder generators are versatile tools that provide power for welding processes and auxiliary functions, making them essential for various industries and remote job sites.
Key factors when choosing a welder generator include power output, fuel type, fuel efficiency, durability, and special features like compact design and integrated equipment.
Safety considerations such as proper grounding, protective gear, and avoiding generator overload are crucial for ensuring safe and efficient welding operations.
Understanding Welder Generators
Engine driven welders are the unsung heroes of the welding world. These versatile machines not only provide the power needed for various welding processes but also offer auxiliary power, air compressor functions, and battery charge/crank assist, making them indispensable on remote job sites. This multipurpose nature ensures that you have all the necessary tools at your disposal, reducing the need for multiple pieces of equipment.
Industries such as farming, ranch maintenance, and even hobbies have embraced the convenience of generator welders. Their portability allows for easy transport to remote locations, ensuring that you can bring your welding capabilities wherever they’re needed. Whether you’re repairing machinery on a farm or undertaking a DIY project, a lincoln welder generator can make the task more manageable and efficient.
Knowing the fuel type of your generator welder impacts its performance and suitability for various environments. Options like gasoline, diesel, and LPG each come with their own set of characteristics and benefits. Diesel, for example, is known for its fuel efficiency and longer run times, making it a popular choice for heavy-duty applications.
Top Lincoln Pipeline Welders
Lincoln Electric is renowned for producing high-quality welding equipment, including some of the best pipeline welders in the industry. Here are some top Lincoln pipeline welders that are highly recommended for their performance and reliability:
Lincoln Electric SAE-300 MP: This engine-driven welder is designed with pipeline welders in mind. It offers excellent arc performance and is equipped with a Perkins diesel engine, ensuring durability and fuel efficiency. The SAE-300 MP is ideal for demanding pipeline welding tasks, providing consistent power and high-quality welds.
Lincoln Electric Vantage 500: Known for its versatility, the Vantage 500 is a multi-process welder generator that can handle stick, TIG, MIG, and flux-cored welding. It features a powerful Cummins engine and offers auxiliary power for additional tools, making it perfect for remote job sites.
Lincoln Electric Pipeliner 200D: Specifically designed for pipeline welding, the Pipeliner 200D offers superior arc characteristics and is built for rugged environments. Its compact design allows for easy transport, and its reliable performance makes it a favorite among pipeline welders.
Lincoln Electric Ranger 305G: This portable welder generator is known for its robust performance and versatility. It provides smooth arc starts and excellent arc control, making it suitable for various welding applications, including pipeline projects.
Lincoln Electric Classic 300D: With a classic design and proven reliability, the Classic 300D is a staple in the pipeline welding industry. It features a powerful engine and delivers consistent welding output, ensuring high-quality welds even in challenging conditions.
These Lincoln pipeline welders are designed with the needs of pipeline welders in mind, offering durability, reliability, and excellent performance across various welding processes. Whether you're working on construction, maintenance, or repair projects, these models provide the power and capabilities required to get the job done efficiently.
Types of Welder Generators
Welder generators come in various types, each suited for different applications. Engine-driven welder generators are commonly used outdoors and can support various welding processes, including stick and TIG welding. These generators are ideal for pipeline welding projects that require consistent and reliable power in remote locations.
Inverter-based welders are another popular option due to their lightweight and compact design. These models are perfect for portable applications where space and weight are critical considerations. Despite their smaller size, inverter-based welders provide high-quality performance, making them a favorite among welders who need to move frequently between job sites.
Hybrid welder generators combine the benefits of engine and utility power, offering flexibility in different work environments. These models can switch between power sources, ensuring continuous operation even if one source becomes unavailable. This adaptability makes hybrid welder generators a versatile choice for various welding projects.
Advantages of Using Welder Generators
Welder generators offer numerous advantages, making them essential for pipeline welding and other applications. One of the primary benefits is their versatility; they combine welding capabilities with portable power generation, allowing for a wide range of uses on job sites. This means you can power your welding tools and other equipment simultaneously, enhancing overall efficiency.
Portability is another significant advantage, especially for mobile applications. Some models are specifically designed to be compact and easily transportable, which is crucial for outdoor construction projects where bringing power to the welding site is impractical. This compact design ensures that you can access your welding operations at different locations without much hassle.
Integrated features in some welder generators, such as compressors or hydraulic pumps, can further enhance their versatility and reduce equipment clutter on-site. Additionally, the auxiliary power output is essential for running additional tools or equipment, making these generators invaluable for complex projects.
Engine-driven welders are particularly suited for outdoor jobs, providing power without reliance on external sources, and are often designed to withstand harsh conditions, ensuring reliability in challenging environments.
Choosing the Right Welder Generator for Your Job
Choosing the right engine driven welder is key to successful welding projects. Matching the generator to the job’s specific requirements, such as welding methods and expected output, is vital. For example, stick welding and TIG welding have different power needs, and your generator must align with these requirements to ensure optimal performance.
Owning a lincoln welder generator can result in significant cost savings by removing the need for multiple power sources. Investing in a versatile and reliable unit reduces operational costs and boosts efficiency. This not only makes your projects more profitable but also ensures that you have the right tools at your disposal for any job.
When selecting a welder generator, consider the specific demands of your projects. Consider the types of welding you’ll be performing, the power requirements, the environmental conditions, and the fuel type. This careful consideration will help you select a generator that meets your needs and enhances your welding operations.
Maintenance Tips for Welder Generators
Regular maintenance is key to ensuring the longevity and optimal performance of welder generators. One of the most critical maintenance tasks is regular cleaning, especially of the air filter and cooling fins. Keeping these components clean helps maintain the generator’s efficiency and prevents overheating, which can lead to costly repairs.
Choosing a welder generator with a reputable engine manufacturer and a robust service network can also contribute to its reliability. Brands like Perkins and Kubota not only provide durable engines but also offer extensive service networks, making it easier to get maintenance and repairs done promptly.
Routine maintenance, such as oil changes, fuel filter replacements, and regular inspections, keeps your generator welder in top condition. Following the manufacturer’s maintenance schedule and promptly addressing issues ensures your generator remains reliable and performs optimally throughout its lifespan.
Popular Welder Generator Models
Lincoln Electric is a leading name in the world of welding equipment, known for producing some of the best pipeline welders in the industry. Their machines are designed with the needs of pipeline welders in mind, offering durability, reliability, and excellent performance across various welding processes.
Lincoln Electric SAE-300 MP: This engine-driven welder is specifically engineered for pipeline welders. It features a Perkins diesel engine, ensuring durability and fuel efficiency, making it ideal for demanding pipeline welding tasks. The SAE-300 MP provides consistent power and high-quality welds, essential for reshaping pipe sections and hot tapping.
Lincoln Electric Vantage 500: This multi-process welder generator is known for its versatility, capable of handling stick, TIG, MIG, and flux-cored welding. Equipped with a powerful Cummins engine, it offers auxiliary power for additional tools, making it perfect for remote job sites and pipeline construction projects.
Lincoln Electric Pipeliner 200D: Designed specifically for pipeline welding, the Pipeliner 200D offers superior arc characteristics and is built for rugged environments. Its compact design allows for easy transport, and its reliable performance makes it a favorite among pipeline welders.
Lincoln Electric Ranger 305G: Known for its robust performance and versatility, this portable welder generator provides smooth arc starts and excellent arc control. It is suitable for various welding applications, including pipeline projects, and offers the power needed for remote job sites.
Lincoln Electric Classic 300D: A staple in the pipeline welding industry, the Classic 300D features a powerful engine and delivers consistent welding output. Its classic design and proven reliability ensure high-quality welds even in challenging conditions, making it a go-to choice for pipeline welders.
These Lincoln machines are designed with the needs of pipeline welders in mind, offering the power, capabilities, and reliability required to get the job done efficiently. Whether you're working on construction, maintenance, or repair projects, Lincoln's welding equipment ensures you have the right tools to enhance productivity and achieve high-quality results.
Safety Considerations When Using Welder Generators
Safety is paramount when using welder generators. Maintaining a proper grounding connection between the workpiece, welding machine, and generator is essential to prevent electric shocks and welding defects. Proper grounding ensures that the electrical circuit is stable, aids in voltage regulation, and reduces the risk of accidents.
Wearing appropriate protective gear, such as a welding helmet and gloves, safeguards against electric shock and welding spatter. Adequate ventilation during welding operations mitigates exposure to harmful fumes and gases. Ensuring that the work area is well-ventilated can protect