What is TIG Welding
Learn to TIG weld
FAQ's TIG Welding
What type of metals can be welded with a TIG welder?
How much does a tig welder cost?
What is a TIG welder?
Are there different types of TIG welding machines available?
Featured Products
Mastering TIG Welding Techniques
TIG welding, or gas tungsten arc welding (GTAW), also known as the TIG process, uses a non-consumable tungsten electrode and an inert gas, argon gas, to achieve precise, high-quality welds with minimal spatter. Perfect for detailed work on metals like stainless steel, aluminum, and nickel alloys, it’s a must-have skill for many industries. In this guide, you’ll learn everything from setting up your equipment to advanced welding techniques, helping you produce top-tier welds.
Key Takeaways
TIG welding, using a non-consumable tungsten electrode, produces high-quality weld quality, spatter-free welds, making it ideal for precise applications in industries like aerospace and pipeline construction.
Understanding the differences between TIG and MIG welding is crucial, as TIG offers lower heat input and greater control, benefiting projects requiring minimal thermal distortion and clean finishes.
Safety measures, including proper ventilation and protective gear, are essential in TIG welding to mitigate the risks posed by UV radiation and toxic fumes during the welding process.
Mastering TIG Welding Techniques
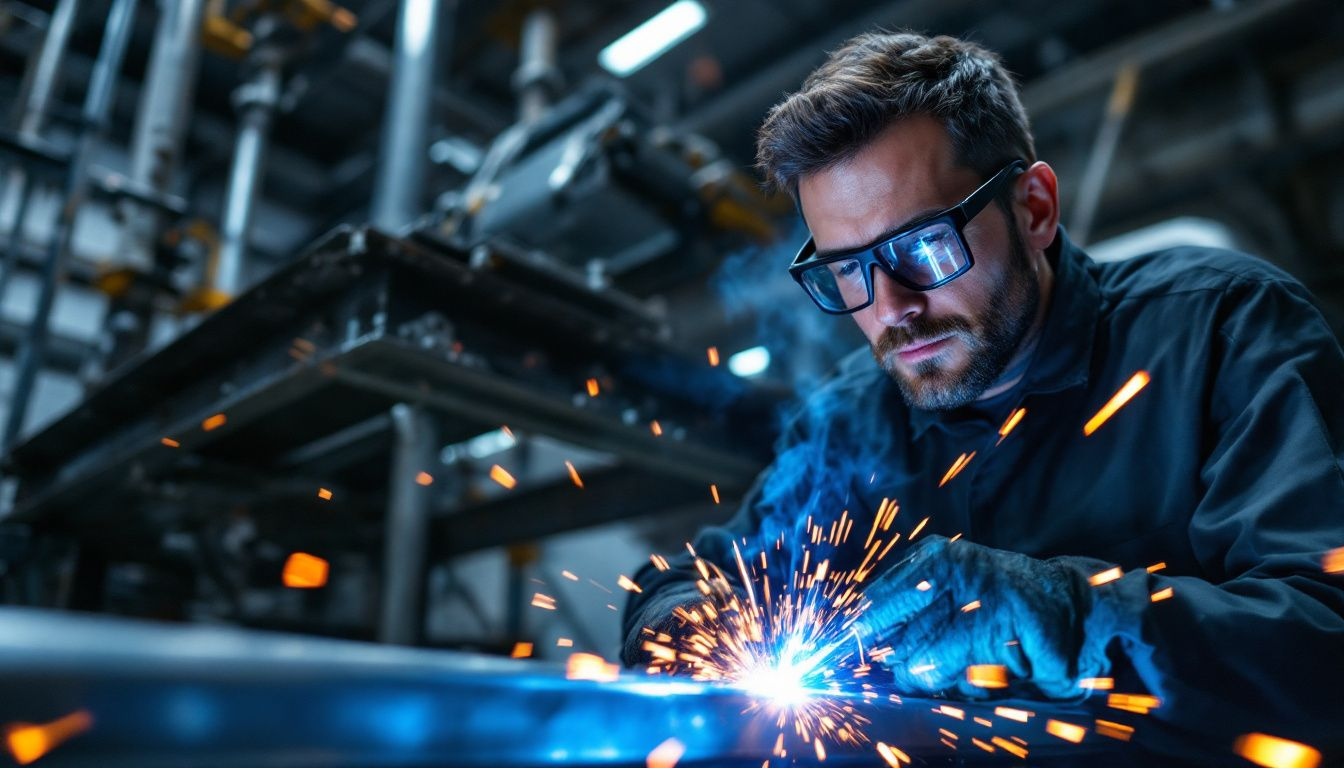
TIG weld, also known as gas tungsten arc welding (GTAW), is a welding process that employs an inert gas and a non-consumable tungsten electrode to join metal pieces. Its versatility and precision make it a staple in industries such as aerospace, pipeline construction, and container manufacturing. The process first found its footing in the aerospace industry in the 1940s and has since become indispensable due to its ability to produce strong, reliable, and aesthetically pleasing welds with minimal spatter, including those made with metal inert gas. Additionally, tig welders are essential for achieving the high-quality results that this process is known for.
The finesse and control offered by TIG welding allow for high-quality, spatter-free welds, making it ideal for applications requiring precision and clean finishes. The precision of TIG welding allows for excellent weld penetration, ensuring strong and durable joints. This technique is particularly suited for welding materials like stainless steel, aluminum, and nickel alloys, ensuring robust and durable joints across various industrial applications. Using filler rods in TIG welding can further enhance control and fill gaps, especially in projects requiring stronger joints between the base metals.
Introduction
Kat de Naoum, a writer and content specialist with over 20 years of experience, brings you this detailed guide on mastering TIG welding techniques. This post aims to provide a comprehensive overview of TIG welding, covering everything from the fundamentals to advanced techniques. You’ll find valuable insights into the equipment, materials, and safety measures essential for successful TIG welding.
Engaging with this content will not only enhance your understanding of TIG welding but also equip you with practical skills to improve your welding projects. Whether you’re looking to refine your techniques or learn the basics, this guide is designed to meet your needs and help you achieve high-quality welds.
The content laid out in this blog post is structured to progressively build your knowledge, starting with the basics and moving towards more complex aspects of TIG welding. You’ll gain a solid foundation and advanced tips to elevate your welding skills.
Understanding TIG Welding
TIG welding stands for tungsten inert gas welding, also known as gas tungsten arc welding (GTAW). The process produces a smooth and consistent weld bead, which is aesthetically pleasing and structurally sound. This process uses a non-consumable tungsten electrode to create an electric arc that joins metal pieces together. The primary characteristic of TIG welding is its ability to produce high-quality, spatter-free welds, which are aesthetically pleasing and structurally sound.
The process involves an inert gas, typically argon, which shields the weld pool from contamination, ensuring a clean and strong weld. Industries such as aerospace, pipeline construction, and container manufacturing rely heavily on TIG welding due to its precision and reliability. Technological advancements have further cemented TIG welding’s place as an irreplaceable technique in various industrial applications.
Key Differences Between TIG and MIG Welding
While TIG welding uses a non-consumable tungsten electrode, MIG welding employs a consumable electrode that melts and becomes part of the weld. TIG welding generally has a slower weld speed compared to MIG welding, but offers greater precision and control. This fundamental difference impacts the applications and outcomes of each welding process. TIG welding generally involves lower heat input, making it suitable for applications that require minimal thermal distortion and precise control.
Aesthetically, TIG welding offers significant benefits, including minimal spatter and less need for polishing, which makes it ideal for cosmetic projects. In contrast, MIG welding is faster but often requires more post-weld cleanup. Additionally, TIG welding equipment, with adjustable settings for gas flow and heat, provides greater versatility for various tasks.
The TIG Welding Process
The TIG welding process begins with setting up the machine, adjusting settings such as current and voltage to suit the specific welding task. Proper preparation of the weld joint is essential for achieving high-quality results. TIG welding can utilize both alternating current (AC) and direct current (DC), with DC Electrode Negative (DCEN) commonly used for ferrous metals. Proper gas pressure is crucial, and a flowmeter regulator is used to ensure effective shielding.
The process employs a non-consumable tungsten electrode that delivers current to the welding arc, creating a stable arc that provides fine control over the weld. The use of shielding gas like argon keeps the weld pool free from contamination, leading to fewer welding defects and a cleaner weld.
TIG welds offer a high degree of control and quality, making them versatile for welding different metals and thicknesses. The TIG welding process allows for precise control over the amperage, which is essential for working with heat-sensitive materials.
Setting Up Your TIG Welder
Setting up a TIG welder involves connecting the welding torch, remote control, and work clamp to the machine. Ensuring that the work lead is connected to the workpiece and using a gas bottle specifically for inert gas are essential steps. Proper tungsten preparation entails grinding the tungsten to a point and ensuring it is clean and free from contamination.
TIG welding machines offer adjustable features that allow for precise control over various weld parameters, making it possible to tailor the setup to the specific requirements of each welding task.
Executing the Weld
Maintaining a short arc length is crucial for better control during the welding process, which improves the overall quality of the weld. Proper technique and control can help minimize weld defects, ensuring a strong and consistent weld. As the arc length increases, the electric arc widens, potentially leading to inconsistent weld quality. Controlling the torch’s travel speed is essential for maintaining consistent weld quality and achieving a uniform bead appearance.
TIG welding is typically slower than MIG and laser welding, emphasizing the need for careful speed management. Common issues such as incomplete fusion can arise from incorrect angles or insufficient heat, and adjusting the welding technique can ensure strong bonds. Additionally, controlling heat input and securing workpieces can reduce the risk of distortion.
Materials Suitable for TIG Welding
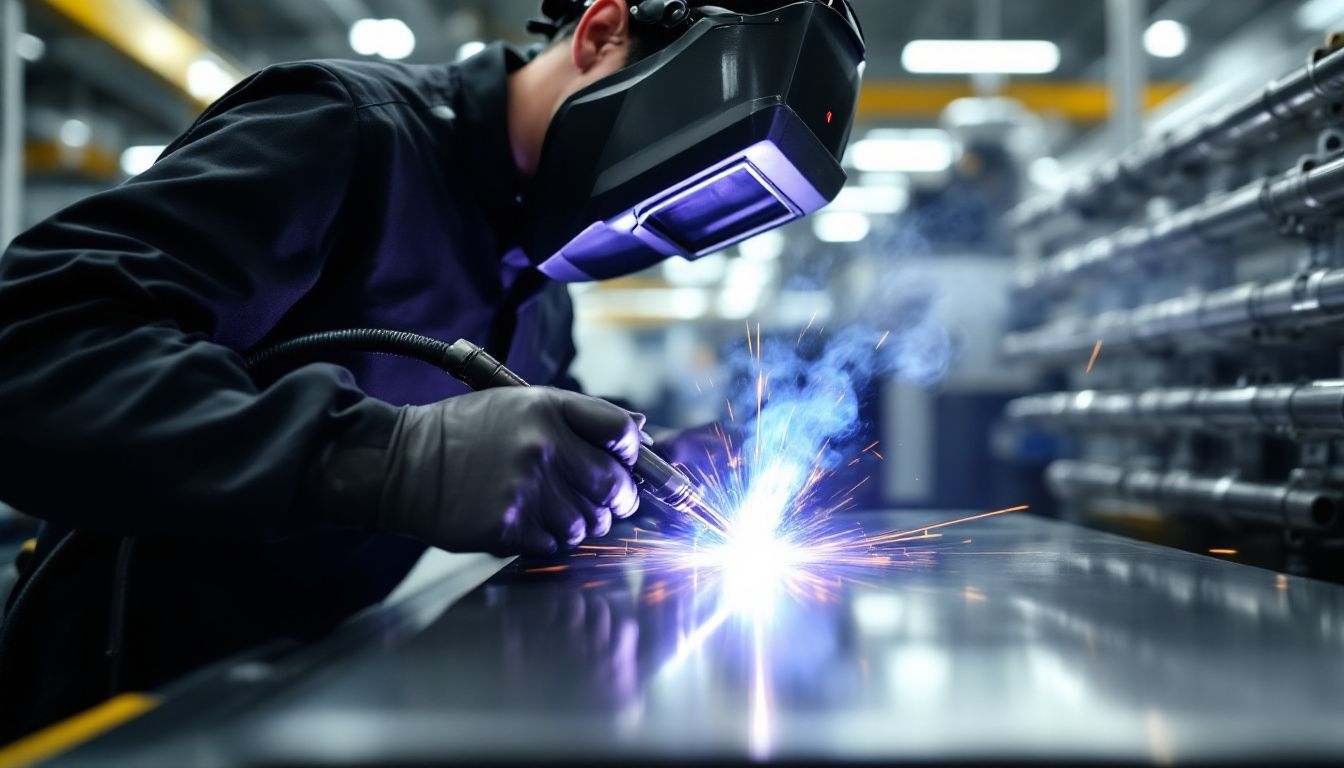
TIG welding is known for its ability to weld multiple metals and alloys, including steel, stainless steel, and aluminum. The weld strength achieved with TIG welding is particularly high, making it suitable for critical applications. A quality TIG welder can produce welds on materials up to 1/4-inch aluminum and 3/8-inch steel or stainless steel. The technique is particularly effective for thin sheets of stainless steel and aluminum, offering precise control of the heat, making it ideal for tig welding steel.
When welding different materials with TIG, factors such as electrode diameter, electric arc applied, and current must be considered to achieve high-quality results. This versatility makes TIG welding a preferred method for various industrial applications.
Stainless Steel
TIG welding provides cleaner welds and low heat input, making it ideal for thin stainless steel materials. Maintaining weld integrity is crucial for achieving high-quality results on stainless steel. For TIG welding stainless steel, a DC with electrode negative polarity is required. Ensuring material cleanliness and controlling gas flow can address issues like porosity in welds, which is often caused by contamination or inadequate shielding gas.
Oxidation and discoloration of welds can be prevented by maintaining proper shielding gas coverage and ensuring the material is clean before welding. These practices lead to high-quality, visually appealing welds on stainless steel.
Aluminum
AC welding is essential for effectively welding aluminum and magnesium. Ensuring proper weld quality is essential for achieving strong and clean welds on aluminum. The purpose of using alternating current in TIG welding aluminum is to provide a cleaning action that removes the oxide film, ensuring a clean weld. This approach is vital for achieving high-quality welds on aluminum, which is known for its oxide layer that can hinder the welding process.
Nickel Alloys
Controlling the heat-affected zone is crucial when welding nickel alloys to maintain the material’s integrity. Controlling the weld pool is essential for maintaining the integrity of nickel alloys. Cracking in welds can occur from rapid cooling or material thickness mismatch, and controlling the cooling rate can help prevent it. Methods to manage heat include controlling welding speed and using appropriate filler material.
These practices ensure high-quality welds on nickel alloys, which are often used in demanding industrial applications due to their excellent performance characteristics.
Choosing the Right Tungsten Electrode
Selecting the right tungsten electrode is crucial for achieving the desired weld characteristics and performance in various applications. The choice of tungsten electrode significantly impacts weld performance and quality. Thoriated electrodes, for example, are known for their ability to handle high currents and maintain their tip shape longer, making them suitable for demanding tasks. Zirconiated electrodes, on the other hand, offer exceptional resistance to contamination and a prolonged lifespan.
The choice of tungsten electrode significantly impacts the quality and effectiveness of the weld, making it essential to understand the different types and their specific applications.
Pure Tungsten Electrodes
Pure tungsten electrodes are suitable for AC current, light metals, and general-purpose work. Pure tungsten electrodes are known for their ability to produce high weld quality in specific applications. They have a smooth and spherical surface characteristic, making them ideal for applications requiring high precision. However, pure tungsten electrodes have a low current carrying capacity and can face ignition problems when used with DC.
Proper maintenance and storage are crucial to minimize electrode deterioration and ensure their effectiveness over time. Grinding techniques should be employed to maintain the electrodes’ condition and performance.
Alloyed Tungsten Electrodes
Thoriated electrodes have a high current capacity and maintain their tip shape longer, although they emit alpha radiation. Rare earth oxide electrodes offer higher durability, very good ignition characteristics, and excel in arc stability with a low erosion rate. Zirconiated electrodes are known for their high resistance to contamination, longer life, and extremely stable arc.
Alloyed tungsten electrodes offer superior weld quality and performance in demanding applications. Understanding the benefits and applications of these alloyed tungsten electrodes helps in selecting the right one for specific welding tasks, ensuring optimal performance and high-quality welds.
Enhancing TIG Welding Efficiency
Welding automation reduces human error and fatigue, leading to faster and more efficient welding processes. Cold wire TIG welding increases productivity and welding speed by allowing for precise and even filler metal feed. Maintaining consistent travel speed is key to achieving uniform weld beads, which directly impacts productivity.
Properly preparing joints and ensuring no excessive gaps can significantly reduce filler metal consumption and improve weld quality, including the management of the weld puddle. Additionally, maintaining welding equipment in good condition prevents inefficiencies that could lead to increased waste and downtime, especially when using a filler rod.
Cold Wire and Hot-Wire TIG Welding
Cold wire TIG welding enhances productivity by allowing for precise and even filler metal feed, which increases welding speed. Both cold wire and hot-wire TIG welding techniques can significantly enhance weld quality. This method is particularly beneficial for applications that require consistent and high-quality welds. Preheating the filler metal in hot-wire TIG welding enhances deposition speed, resulting in quicker welds and improved productivity.
The increased deposition speed in hot-wire TIG welding results in more consistent welds due to faster metal transfer and less heat distortion. This technique is ideal for projects that demand high efficiency and minimal heat-affected zones, ensuring high-quality outcomes.
Orbital Welding
Orbital welding is a technique that excels in maintaining high seam quality for various industrial applications. Orbital welding is known for its ability to produce consistent and high weld quality. In this process, a fixed pipe setup allows for a movable TIG torch, facilitating precise and consistent welds. The consistent seam quality achieved through orbital welding makes it ideal for use in pipelines and other critical infrastructure, where reliability and precision are paramount.
The ability to produce high-quality welds with minimal spatter and excellent seam appearance makes orbital welding a preferred method in industries that require stringent quality standards. This technique ensures that welds are not only structurally sound but also aesthetically pleasing.
Safety Considerations in TIG Welding
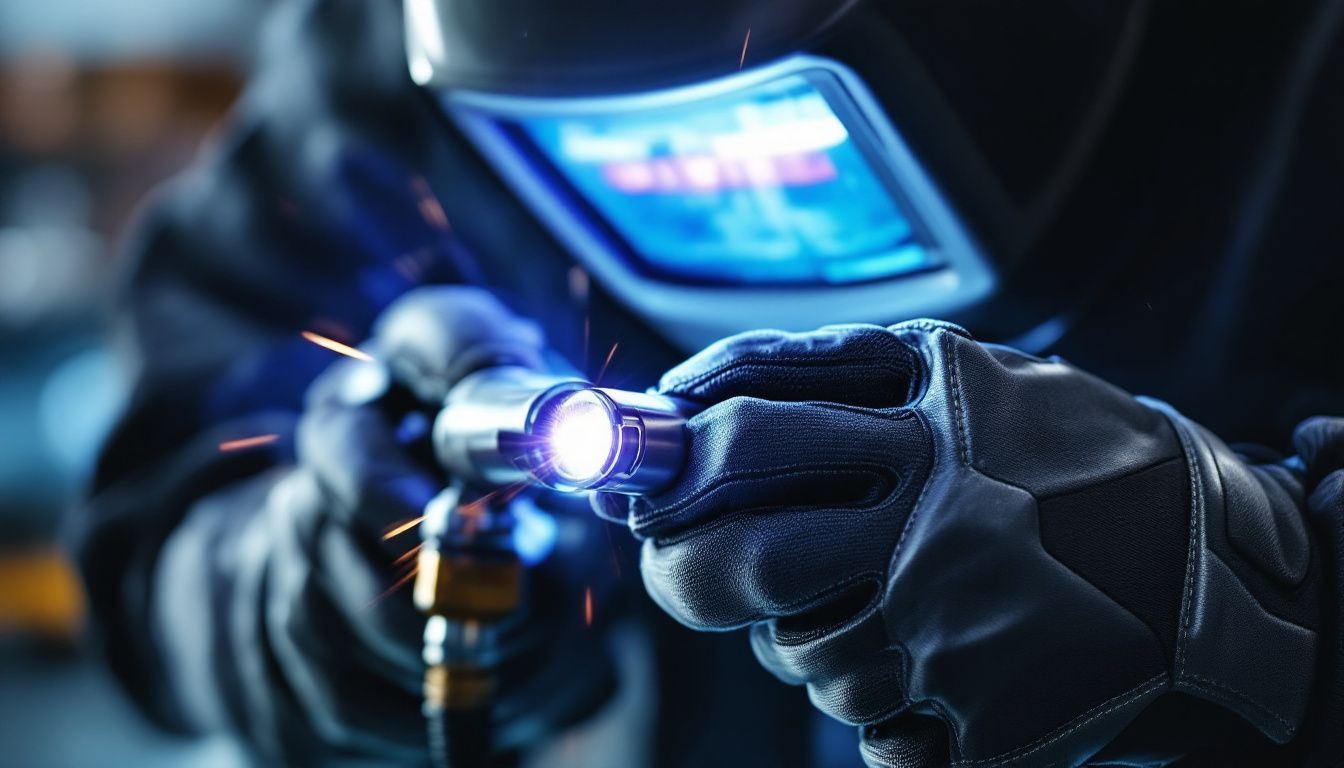
Safety is paramount in TIG welding, given the intense UV radiation emitted during the process, which is more potent than sunlight and can cause serious eye injuries. Ensuring safety is crucial for maintaining high weld quality and preventing defects. Wearing gloves and long-sleeve shirts is essential to protect the skin from harmful UV exposure. Exposure to toxic fumes from molten metals also poses significant risks to respiratory health, making proper ventilation crucial.
Argon and carbon dioxide, commonly used as shielding gases, can displace oxygen in confined spaces, posing a suffocation risk. Ensuring adequate ventilation and using protective gear like welding helmets and respirators are critical for maintaining a safe working environment.
Troubleshooting Common TIG Welding Issues
Common issues in TIG welding include porosity, which occurs due to air pockets when the torch angle is not properly adjusted. Maintaining a proper forward angle with the TIG torch can prevent air pockets and reduce the risk of porosity in welds.
Overwelding, or creating larger welds than necessary, can lead to increased costs and potential weld failure due to excess heat. To maintain weld quality, it is essential to ensure appropriate bead size and technique, avoiding excessive heat that can compromise weld integrity.
Addressing these common issues with proper techniques and adjustments can significantly improve the quality and reliability of your welds.
Summary
In summary, mastering TIG welding involves understanding the intricacies of the process, selecting the right materials and electrodes, and employing advanced techniques to enhance efficiency. From setting up your TIG welder to executing the weld and troubleshooting common issues, this guide provides a comprehensive overview to help you achieve high-quality welds.
By applying the knowledge and tips shared in this guide, you can elevate your welding skills and produce impeccable welds that meet industrial standards. Embrace the art and science of TIG welding, and let your craftsmanship shine in every project you undertake.
Frequently Asked Questions
What is TIG welding?
TIG welding, or gas tungsten arc welding (GTAW), is a precise process that employs an inert gas and a non-consumable tungsten electrode to create high-quality, spatter-free welds in metal fabrication. This technique is favored for its clean and strong results.
How does TIG welding differ from MIG welding?
TIG welding utilizes a non-consumable tungsten electrode for precision and lower heat input, while MIG welding employs a consumable electrode, allowing for faster processes at the expense of potentially more post-weld cleanup.
What materials can be welded with TIG?
TIG welding can effectively join various metals and alloys, including steel, stainless steel, aluminum, and nickel alloys. This versatility makes it a preferred choice for many applications.
How do you set up a TIG welder?
To set up a TIG welder, connect the torch, remote control, and work clamp to the machine, ensuring the work lead is attached to the workpiece. Prepare the tungsten electrode by grinding it to a point. This will ensure optimal performance for your welding tasks.
What safety precautions should be taken in TIG welding?
To ensure safety in TIG welding, always wear appropriate protective gear, provide adequate ventilation to minimize fume exposure, and handle shielding gases properly to avoid oxygen displacement in confined areas.