What is MIG Welding
MIG welding (Metal Inert Gas welding) is a popular welding process that uses a continuously fed wire electrode and shielding gas to join metals. The wire melts as it is fed through the gun, creating clean, strong welds.
Ideal for beginners and professionals, MIG welders like wire feed welders, gas MIG welders, and portable MIG welders offer efficiency and versatility. Commonly used for mild steel, stainless steel, and aluminum, MIG welding is perfect for automotive repairs, fabrication, and DIY projects.Learn to MIG weld
Learning to MIG weld is simple and rewarding for beginners and professionals alike. MIG welding (Metal Inert Gas welding) uses a wire feed system and shielding gas to produce clean, strong welds. Start with a wire feed welder or a portable MIG welder for easy handling and versatility.
Perfect for automotive repairs, fabrication, and DIY projects, MIG welders are ideal for welding mild steel, stainless steel, and aluminum. With practice, anyone can master MIG welding techniques.
MIG Welding Wire
MIG welding wire is essential for producing clean, durable welds in MIG welding machines. Designed for various metals like mild steel, stainless steel, and aluminum, MIG wire ensures smooth wire feeding and consistent results.
Choosing the right MIG welding wire improves weld quality and efficiency. For mild steel, ER70S-6 wire is ideal, while aluminum projects require specialized options. Whether you’re using a wire feed welder or a gas MIG welder, quality wire matters.
FAQ's MIG Welding
1. What is a MIG Welder, and How Does It Work?
2. What’s the Difference Between a Wire Feed Welder and a MIG Welder?
3. What Are the Best MIG Welders for Sale Near Me?
4. How Much Does a MIG Welder Cost?
To get started with MIG welding equipment, you’ll need:
- MIG welding guns and torches
- MIG welding kits
- MIG consumables like tips, nozzles, and wire
- MIG welding carts and undercarriages for portability
Shop for MIG welding supplies for sale to complete your setup.
Featured Products
Mastering MIG Welding: Tips and Techniques for Beginners
Metal inert gas (MIG) welding uses an electric arc to join metals and is known for its speed and ease of use. This makes it perfect for beginners and experienced welders. This article covers the basics of MIG welding, the equipment you’ll need, essential techniques, and safety tips.
Key Takeaways
MIG welding is a fast and versatile welding method that combines a continuously fed wire electrode with shielding gas for high-quality welds.
Essential equipment for MIG welding includes a MIG welder, wire electrodes, and appropriate shielding gases, each contributing to the welding process’s quality and efficiency.
Safety is paramount in MIG welding; proper safety gear and maintaining a safe workspace help prevent accidents and ensure a productive environment.
Understanding MIG Welding
Metal inert gas (MIG) welding, also known as gas metal arc welding, utilizes a welding arc to join metals and has been a staple in the welding industry since its development in the 1940s. Unlike other welding methods, MIG welding uses an electric arc to melt the wire and metal pieces, fusing them together in a process that’s both efficient and versatile. This process is favored for its speed, ease of learning, and ability to produce high-quality welds consistently.
This part will highlight what makes MIG welding unique and compare it to other popular welding processes. Recognizing these differences clarifies why MIG welding is often preferred for many applications.
What is MIG Welding?
Metal inert gas (MIG) welding is a process that uses electricity to melt and join metals. The technique involves a continuously fed wire electrode, which acts as both the filler material and the electrode, allowing for efficient melting metals and deposition into the weld pool, controlled by the welding torch. A key component of the metal inert gas mig welding process is the shielding gas, which protects the molten metal from atmospheric contaminants, ensuring a high-quality weld.
One of the primary advantages of MIG welding is its speed and versatility. It’s particularly well-suited for beginners due to its straightforward setup and operation. Properly adjusting the arc length is crucial for maintaining a stable weld puddle and achieving high-quality welds. When executed correctly, MIG welding can produce consistent and high-quality welds, making it a popular choice for both industrial applications and DIY projects.
MIG vs. Other Welding Methods
When comparing MIG welding to other methods like TIG (Tungsten Inert Gas) welding, several differences stand out, particularly in the use of the welding arc. MIG welding uses a consumable electrode that acts as the filler material, which simplifies the process and makes it faster than TIG welding. In addition to MIG welding, there is also Metal Active Gas (MAG) welding, which uses active shielding gases that can alter the chemical composition of the weld. This speed and efficiency make MIG welding ideal for welding thicker materials and high-productivity environments.
Another significant advantage of MIG welding is its cleanliness. Unlike stick welding, which produces a lot of spatter and slag, MIG welding is relatively clean. This cleanliness, combined with its ability to weld various metals including carbon steel and stainless steel, makes MIG welding a versatile and attractive method for many applications.
Essential Equipment for MIG Welding
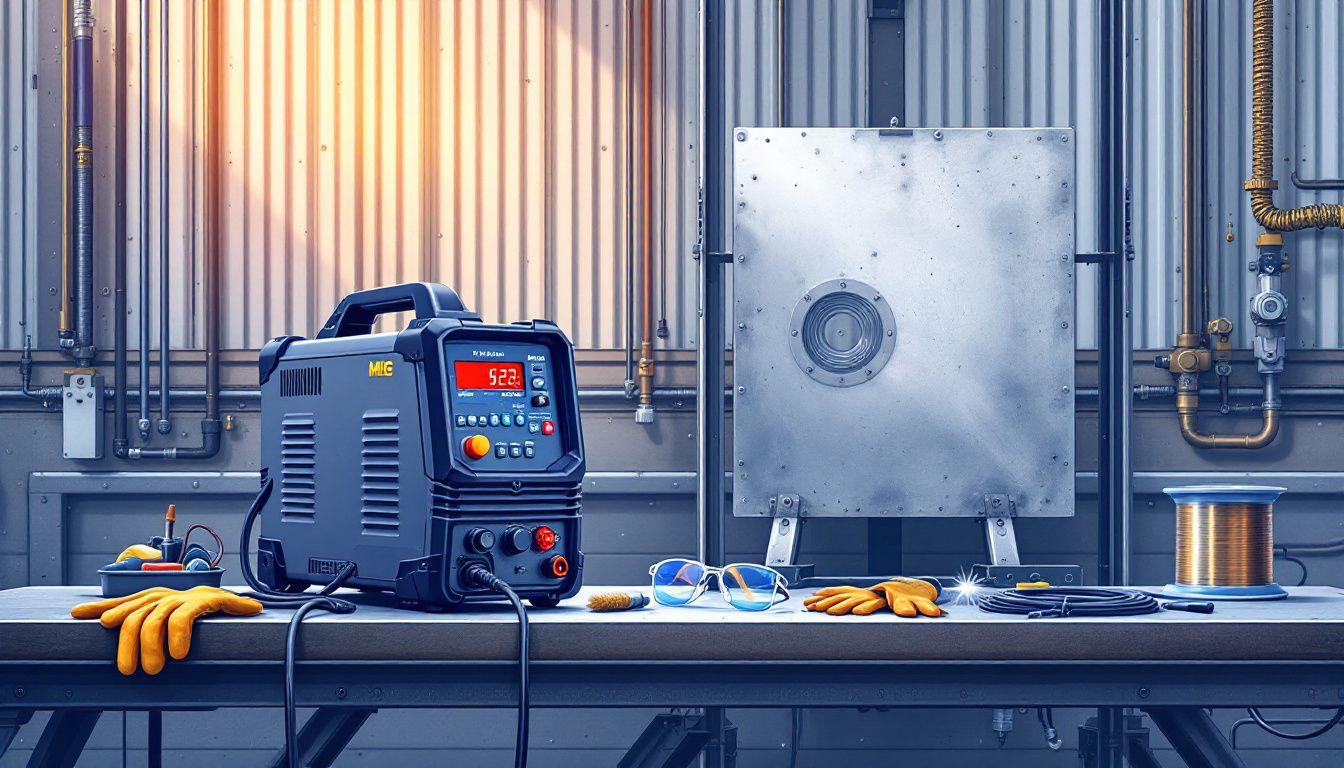
To get started with MIG welding, you’ll need some essential equipment. This includes a MIG welder, wire electrodes, and shielding gases. These components work together to ensure a smooth and efficient welding process. Each piece of equipment plays a crucial role in the overall quality and efficiency of your welds, making it important to understand their functions and how to use them properly.
In this section, we’ll delve into the details of each essential component, helping you make informed decisions about the equipment you need for successful MIG welding projects.
The MIG Welder
The MIG welder is the heart of the MIG welding setup. It converts electrical energy to deliver the necessary current for welding. Key components of the MIG welder include rollers that ensure consistent wire feeding to the welding torch and the welding torch itself, which maintains precise control over the weld puddle.
Understanding these components and how they work together is essential for achieving high-quality welds.
Wire Electrodes
Wire electrodes are a critical component of the MIG welding process. There are two basic types of wire electrodes used in MIG welding: hard wire and flux-cored wire. Hard wire is typically used with a shielding gas mixture, while flux-cored wire generates its own shielding gas, making it suitable for outdoor work. Selecting the right wire electrode depends on the material being welded and the specific requirements of the project.
For example, welding aluminum requires aluminum wire and typically higher amperage settings due to its thermal conductivity. On the other hand, mild steel can be welded with hard welding wire and a common gas mixture of argon and CO2.
Choosing the right wire diameter is also crucial; thinner wires are ideal for welding thin metals, while thicker wires are better suited for welding thicker materials.
Shielding Gases
Shielding gases play a vital role in MIG welding by preventing atmospheric contamination during the welding process. Commonly used gases include argon, helium, and carbon dioxide, either used individually or in mixtures. While inert gases like argon and helium provide clean welds, non-inert gases like carbon dioxide can offer deeper penetration but may result in more spatter.
Choosing the right shielding gas depends on the material being welded and the desired weld quality.
Preparing for MIG Welding
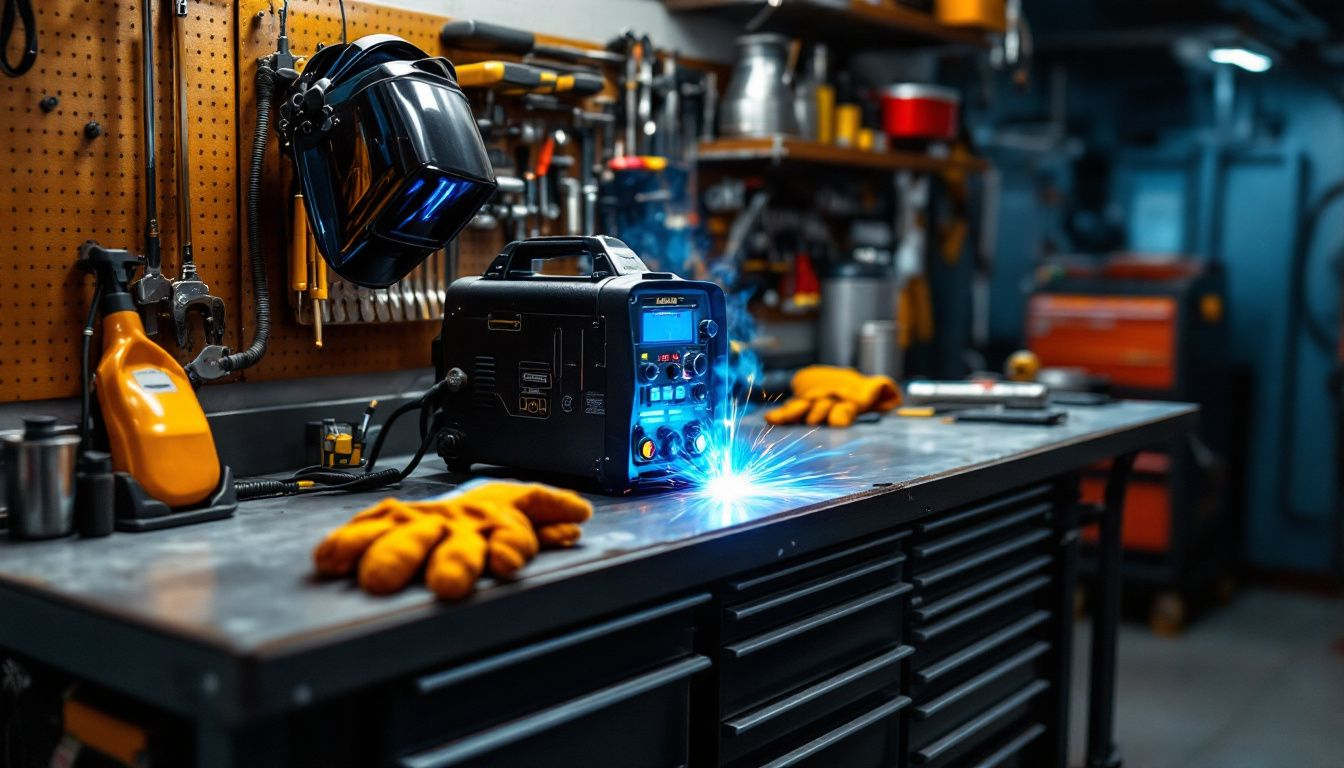
Preparation is key to successful MIG welding. Before you even strike an arc, it’s essential to ensure your workspace and materials are ready. Proper preparation not only ensures the quality of your welds but also enhances safety. This section will cover the crucial steps of cleaning and preparing your work surfaces, as well as setting up your MIG welder for optimal performance.
These preparation steps help establish a solid foundation for your welding projects, reducing issues and enhancing outcomes.
Surface Preparation
Clean metal surfaces are critical for strong welds. Before you start welding, use a metal brush or grinder to remove rust, paint, and other contaminants from the surfaces to be joined. Ensuring that your metals are clean and free from impurities will help achieve high-quality welds.
Proper joint preparation, including grinding down edges, is also essential for a clean and strong weld.
Setting Up the Welder
Setting up your MIG welder correctly is crucial for achieving high-quality welds. Start by opening the shielding gas valve and checking the gas flow at around 20 ft³/hr. Ensure the welder is powered on, attach the grounding clamp, and set the proper wire speed and power settings based on the material thickness and type.
Proper wire feed speed adjustment is crucial to avoid burn-through and achieve a solid weld.
MIG Welding Techniques
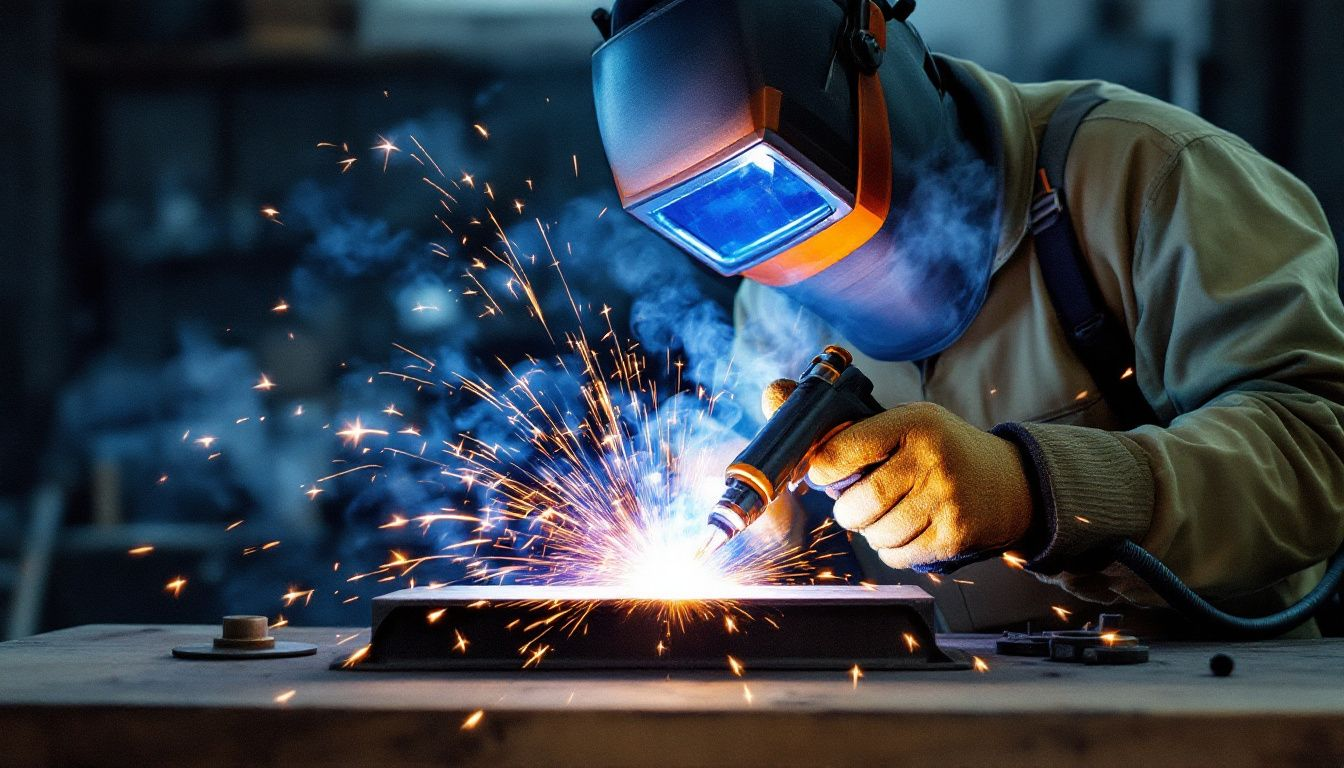
Mastering MIG welding techniques is essential for producing strong and visually appealing welds. From laying a bead to understanding different welding positions and metal transfer modes, each technique requires practice and precision. This section will provide an overview of these techniques, helping you refine your skills and achieve better results in your welding projects.
Incorporating these techniques into your practice enables you to tackle various welding tasks with confidence and expertise.
Laying a Bead
Laying a uniform bead is a fundamental skill in MIG welding. Maintaining a steady hand and consistent speed is crucial for achieving a clean weld bead. Keep a consistent distance between the contact tip and the workpiece to control penetration and minimize spatter.
Position the arc on the leading edge of the weld puddle, and for butt joints, hold the welding gun at a 90-degree angle.
Welding Positions
Different welding positions require adjustments in technique to achieve optimal results, and the MIG welding torch is capable of managing horizontal, vertical, and flat welding positions. Each of these positions presents its own unique challenges. For horizontal and flat positions, the travel angle generally remains the same, while vertical welding requires reducing voltage and amperage by 10 to 15%.
When welding overhead, ensure the weave beads are not too wide and maintain fast travel speeds to prevent weld metal from falling out of the joint. For multi-pass welds on thick metal, weaving techniques can be used to fill the weld joint effectively.
Metal Transfer Modes
Metal transfer modes in MIG welding refer to how the filler metal is processed through the welding arc into the weld puddle. The main transfer modes include short circuit, globular, and spray transfer.
Short-circuit welding occurs when the wire touches the weld pool, creating electrical short-circuits. Globular transfer involves higher current and voltage, producing larger molten metal droplets and more spatter. Spray welding, on the other hand, offers high deposition rates with minimal spatter, making it ideal for thicker materials.
Common Challenges and Solutions
Every welder faces challenges, but understanding common issues and their solutions can make a significant difference. This section will address some of the most common challenges in MIG welding, such as spatter, burn-through, and inconsistent welds, providing practical solutions to help you overcome these obstacles.
Understanding how to handle these challenges better equips you to consistently achieve high-quality welds.
Dealing with Spatter
Spatter is a common issue in MIG welding, caused by excess molten droplets from the electrode wire bonding with the metal, and can be minimized by maintaining a consistent travel angle with the welding gun.
Good practice techniques, such as proper wire feed speed and voltage settings, can also help reduce spatter and improve weld quality.
Preventing Burn-Through
Burn-through occurs when the weld metal penetrates completely through thin base materials, often due to excessive heat. To prevent burn-through, reduce the voltage or wire feed speed while increasing the travel speed.
If burn-through does happen, you can correct it by tacking new material onto the existing surface and allowing it to cool between applications.
Fixing Inconsistent Welds
Inconsistent welds can result from various factors, including contaminants on the metal, low wire speed, or incorrect power settings. To achieve consistent welds, ensure your metal is clean and free of impurities.
Adjust your travel speed and wire feed to match the joint thickness, and keep a log of successful settings to replicate high-quality welds across different projects.
Safety Considerations in MIG Welding
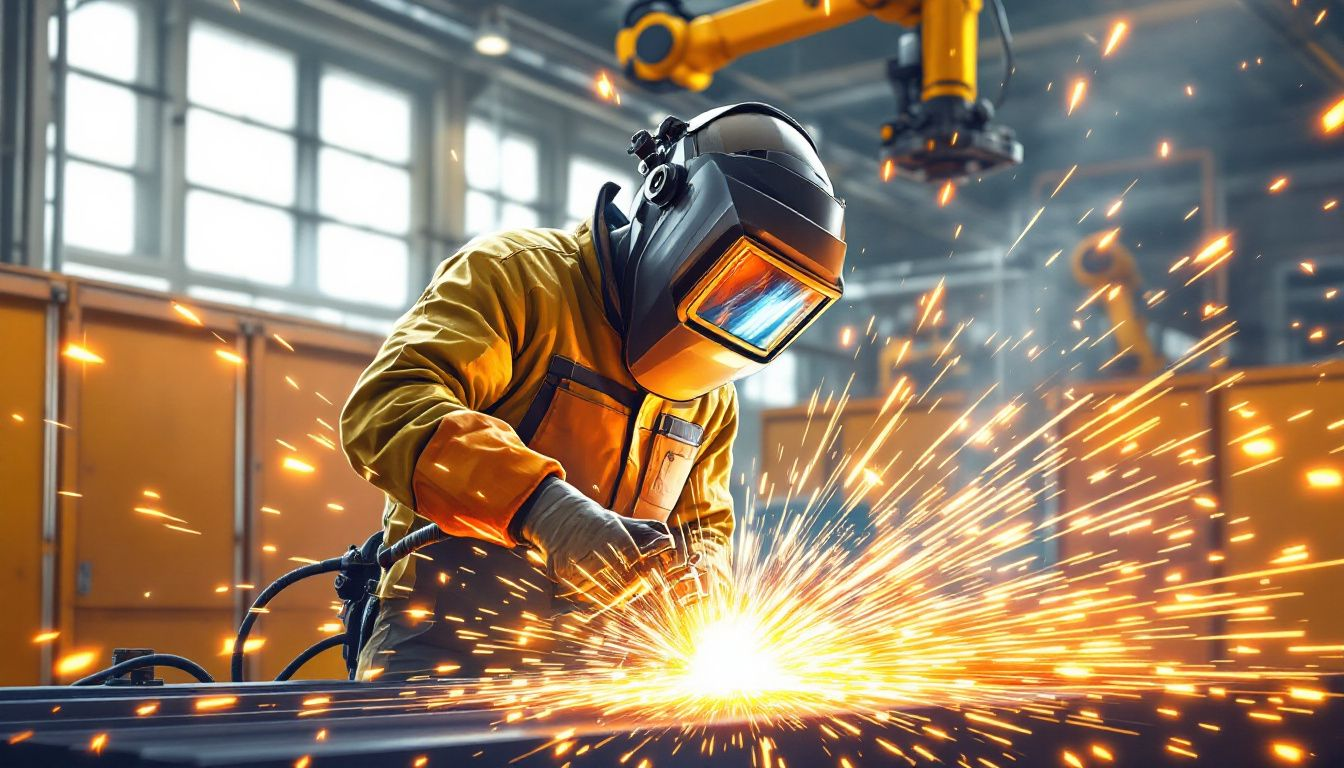
Safety should always be a top priority in MIG welding. Proper safety measures not only protect the welder but also ensure a safe working environment. This section will cover the essential safety gear needed for MIG welding and safe workspace practices to minimize risks and hazards.
Adhering to these safety guidelines ensures a productive and accident-free welding experience.
Essential Safety Gear
Wearing the right safety gear is crucial for protecting yourself while welding. This includes using quality welding helmets to shield your face from sparks and UV radiation. MIG safety gloves and flame-resistant clothing are also essential to protect against burns.
Additionally, using masks and respirators that meet safety standards will help protect against harmful fumes.
Safe Workspace Practices
Maintaining a safe workspace is just as important as wearing safety gear. Ensure your welding area is free from flammable liquids and gases to prevent fire hazards. Regularly inspect and maintain your welding equipment to minimize the risk of malfunctions. Proper ventilation is crucial to reduce the accumulation of toxic fumes during MIG welding.
Additionally, having a suitable fire extinguisher, such as a CO2 extinguisher, readily accessible can be a lifesaver in case of emergencies.
Advanced Tips for Experienced Welders
For those who have mastered the basics of MIG welding, advanced techniques can significantly enhance the quality and efficiency of your work. This section will provide tips for optimizing weld quality and welding different metals, helping you take your welding skills to the next level.
Incorporating these advanced tips allows you to tackle more complex projects with confidence and precision.
Optimizing Weld Quality
Optimizing weld quality involves fine-tuning various aspects of the welding process. Adjusting the welding arc to match your personal preferences can enhance control and the appearance of the weld. Consistent practice and experimentation with different settings and techniques will lead to improved welding outcomes.
Advanced techniques allow welders to address specific challenges, resulting in higher quality and efficiency.
Welding Different Metals
MIG welding’s versatility makes it suitable for various materials, including mild steel, stainless steel, and aluminum. Welding aluminum, for instance, requires higher amperage settings due to its thermal conductivity. Different metals may also require distinct filler materials and shielding gases to ensure compatibility and effective bonding.
Understanding these requirements will help you achieve strong and durable welds across different materials.
Summary
Mastering MIG welding involves understanding the process, using the right equipment, preparing properly, and honing your techniques. From laying a bead to dealing with common challenges, each step is crucial for producing high-quality welds. Safety is paramount, and wearing the correct gear and maintaining a safe workspace cannot be overemphasized.
As you continue to practice and apply these tips, you’ll find that your skills and confidence grow. Whether you’re welding for a hobby or professionally, the knowledge and techniques shared in this guide will set you on the path to success. Remember, welding is as much an art as it is a science, so keep experimenting and refining your craft.
Frequently Asked Questions
What is the main advantage of MIG welding for beginners?
The main advantage of MIG welding for beginners is its ease of learning and efficiency, allowing newcomers to quickly develop their skills. This streamlined process fosters a rapid understanding of welding techniques.
How do I choose the right wire electrode for my project?
To choose the right wire electrode for your project, focus on the material being welded and its thickness; use thinner wires for lighter materials and thicker wires for heavier materials. This ensures optimal performance and quality in your welding work.
What are the common shielding gases used in MIG welding?
Common shielding gases used in MIG welding are argon, helium, and carbon dioxide, either individually or in various mixtures. These gases help protect the weld from contamination and improve the overall quality of the weld.
How can I prevent burn-through when welding thin metals?
To prevent burn-through when welding thin metals, it is essential to reduce the voltage or wire feed speed while increasing the travel speed. This approach will help you maintain control and achieve a clean weld without compromising the material.
What safety gear is essential for MIG welding?
The essential safety gear for MIG welding includes a welding helmet, MIG safety gloves, flame-resistant clothing, and a respirator to safeguard against harmful fumes. Prioritizing this equipment is crucial for ensuring your safety while welding.